Business Services Customer Spotlight
Service Spotlight on Custom Projects: ACRT Services
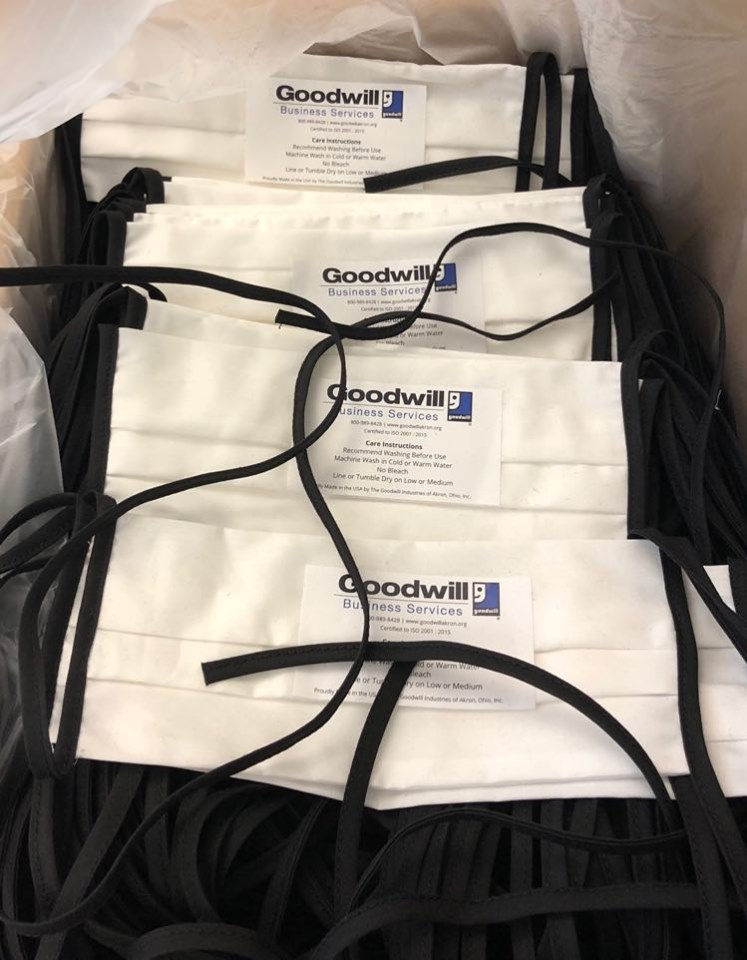
Earlier this year, ACRT Services executive team was looking for a way to get protective masks for employees working in the field throughout the country. The ACRT Services family of companies — ACRT, ACRT Pacific, and Bermex offer expert, independent consulting solutions to utilities and associated organizations. Brad Schroeder, chief financial officer at ACRT Services, volunteered to reach out to Goodwill to see what they could do.
Schroeder previously served on the board of directors for Goodwill and had toured their facilities in the past, which included its industrial sewing facility. As he was familiar with the sewing services that they provide, he called Nan McClenaghan, president and CEO of Goodwill Industries of Akron and a member of the ACRT Services board of directors, and asked if its sewers could possibly make masks for ACRT Services and their family of companies.
Working on A Solution
ACRT Services’ goal was to provide employees with five to six masks so they could be rotated while working or shared with family members. McClenaghan reached out to Al Sardelle, her sewing manager, who immediately began reviewing patterns for the masks.
“We had cotton in inventory that would normally be used for other products,” McClenaghan said. “We took anything we could find that would be close to that and got to work on prototypes.”
Goodwill Industries had a conference call with the ACRT Services team on Monday, April 6 to share the prototypes they’d created. By Friday, April 10 of that week, Goodwill had delivered the first 500 masks to ACRT Services. All 500 were completed by Tanya and Kathy along with Sardelle.
“It’s a simple mask once you get the pattern down,” McClenaghan said. “It’s made to be high quality but also to be produced in high volumes. Al, Tanya, and Kathy worked out how we could do that in a very consistent, high-quality way while producing a large number of masks at the same time.”
Goodwill had been reaching out to different companies offering their industrial sewing services, but until ACRT Services called, it hadn’t received any responses. In total, ACRT Services ordered 2,000 masks made of unbleached cotton and then an additional 7,000 made of quilters cotton.
“We cleaned out our supplier,” McClenaghan said. “We bought a lot more material than we’ve ever bought before. We were afraid that cotton wouldn’t be available.”
Partnering Together
In gratitude for Goodwill’s quick support and turnaround, and to support its mission of helping people prepare for, find and retain employment, ACRT Services provided Goodwill with an operating donation of $15,000.
“Unfortunately, at that time, we had no retail operations revenue coming in and very few people working,” McClenaghan said. “While our sewing team and the assembly team had been working, until mid-May, we still had a large amount of our staff furloughed. The grant ACRT Services provided us with has supported us during this difficult time, and we’re very grateful for it.”
It remains that many organizations and their employees will continue to rely on — and be required to use — face masks in order to protect themselves and their customers.
“People are going to need reusable cloth masks for a long time,” McClenaghan said. “We plan to continue making those and remain available to support organizations looking for face masks and other industrial sewing products. We are very grateful that ACRT Services called us and allowed us to work out a strong base pattern. That trust in Goodwill’s sewing team set the stage for all the additional orders that came after ACRT Services’.”
Goodwill sewers produced many face masks through August. It worked on masks for Cardinal Safety Products, MAGNET for the State of Ohio and many other customers, as well as community masks funded by GAR Foundation and United Way of Summit County. By the end of summer, the sewing team created and shipped more than 50,000 masks.
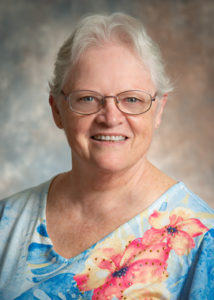
Kathy Martin
About Goodwill Industries of Akron Sewing Team
Kathy Martin started in the business services division of Goodwill in June of 2013. Prior to working at Goodwill, Kathy worked at Belaire Products, Inc. in Akron from 1994 until 2012. She is an experienced seamstress and is an expert on all of Goodwill’s sewing equipment. Kathy also helps with sample making and special projects. She has two adult children and three grandchildren. Kathy enjoys crocheting and spending time with her family.
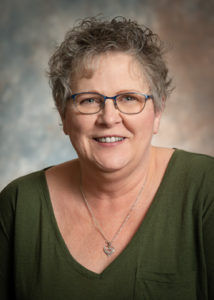
Tanya Oaks
Tanya Oakes started with Goodwill in June of 2004. Before joining the Business Services team, Tanya worked at Ideal Draperies in Barberton for 10 years. She was a production seamstress and was promoted to Sewing Group Leader in early 2019. Tanya is an expert seamstress and pattern maker. She makes all Goodwill’s prototypes and does all of its time studies. Tanya has two adult children — her son is an airline pilot, and her daughter is a nurse practitioner. She has been married for 38 years and hopes to be a grandmother soon. Tanya likes quilting in her spare time.
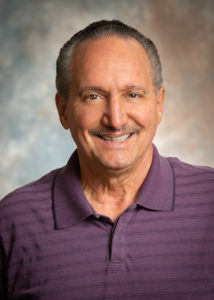
Al Sardelle
Goodwill Sewing Manager Al Sardelle has been working at Goodwill Industries of Akron for 16 years. He has more than 40 years of experience in the apparel and textile industries. Prior to coming to Goodwill, Al worked at several needle trade companies including Frisch Knitting Mill, Bobbie Brooks, Dalton Industries, and North American Knitting Company. Al has two adult children and one grandson. He enjoys playing tennis and spending time with his family.
Service Spotlight on General Machine Corporation
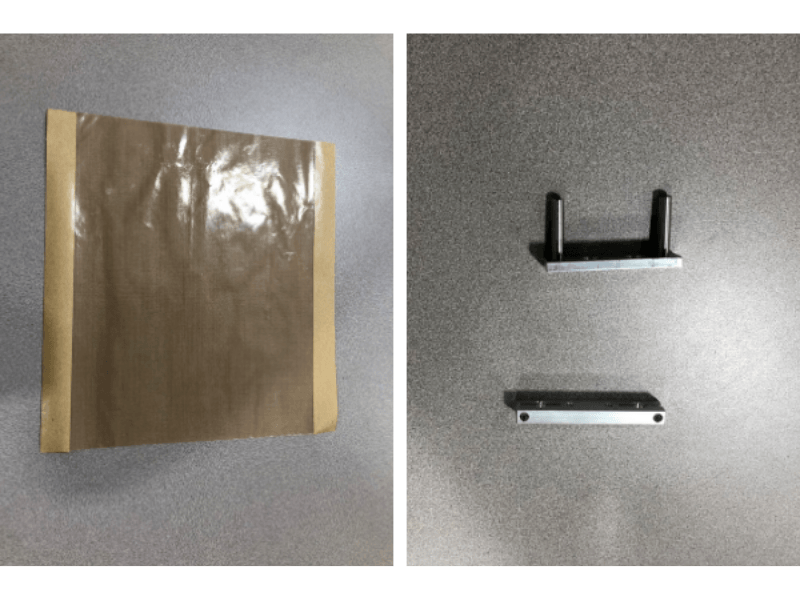
Goodwill Industries of Akron (GIA) has a symbiotic relationship with General Machine Corporation as it is both a vendor and a customer of GIA. One of the parts that GIA makes for General Machine Corporation is a 12” x 12.5” Teflon sheet with 2 strips of 12.5” double sided Teflon tape adheres to both side of sheet. These are usually used in a heated press application. During this General Machine Corporation contract, GIA has had program participants either cutting the sheets or applying the tape at one time or another. This work allows program participants to build work skills on a real customer’s job and display their adherence to GIA’s work instructions and ISO procedures. The participant can then document this experience on a resume and move onto external competitive employment when the time is right for that program participant.
As GIA’s vendor, General Machine Corporation is the source for the male and female bracket, a product that GIA uses in assembling the deflator for another customer.
GIA is very pleased that it has been able to serve General Machine Corporation’s business needs for about three years and it was honored that another GIA customer referred GIA to General Machine Corporation.
Service Spotlight on Automated Packaging Systems, Inc.
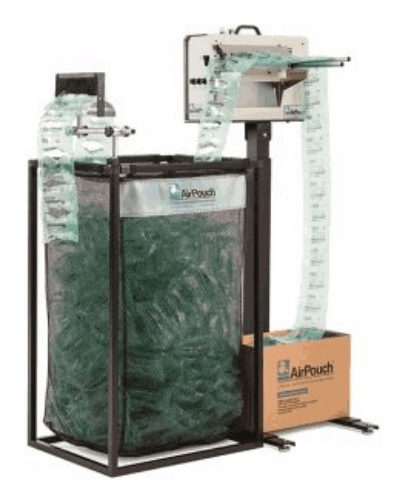
Since 2004, Goodwill has been a valued partner to Automated Packaging Systems, Inc. (APS), a world leader in designing and manufacturing flexible bag packaging systems for more than 50 years. The company, headquartered in Streetsboro, Ohio, works with Goodwill to make custom hoppers and carts for its automated packaging systems as well as many other assembly jobs (deflaters, seal pads, protective cable sleeves, Teflon cover strip, sealer block and refab Housing).
It is a unique customer because it uses both industrial sewing and light assembly services for its custom hoppers and carts. In 2018, Goodwill worked on 619 hoppers and 90 carts through the teamwork within its Business Services division, which is now certified to ISO 9001: 2015 without design Certificate Number: 07.190.1.
In August 2019, APS was acquired by Sealed Air, a leading manufacturer of protective packaging solutions. The acquisition of APS will allow Sealed Air to better serve the e-commerce, fulfillment and food packaging markets. APS brings highly complementary and additive capabilities to Sealed Air, including expertise in engineering, automation technology and sustainability.
Goodwill’s Business Services team wishes its valued partner, APS, and its new owner, Sealed Air, continued success in all their endeavors!
Service Spotlight on GOJO- PROVON Nail Cleaners
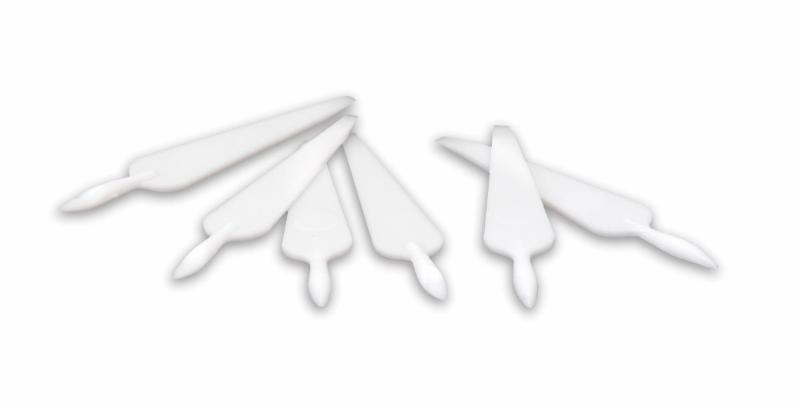
GIA is grateful to have GOJO Industries, Inc. as a long-time customer assisting with many different projects over the years. Currently, one service Goodwill provides is the acquisition and packaging of surgical nail picks. Besides product specifications, GOJO supplies a copy of its ISO instructions and Goodwill incorporates the core aspects into its own detailed work instructions to assure a correct and consistent outcome for GOJO’s product.
Goodwill is honored to be a GOJO supplier and have the opportunity to use this and other customer fulfillment endeavors to help individuals build work skills in an ISO certified production environment.